Comprehensive Overview to Effective Packaging Machine Fixing Strategies for Optimal Efficiency
Reliable product packaging maker fixing is important for preserving functional continuity and item high quality in today's fast-paced manufacturing setting. Employing an organized method to diagnostics and repair, together with preventive maintenance methods, can substantially enhance maker longevity and performance.
Typical Packaging Machine Concerns
Product packaging makers, essential for effective production lines, often experience a number of common problems that can disrupt procedures. One common problem is imbalance, which can cause incorrect sealing or identifying, eventually influencing item integrity and discussion. This imbalance might come from damaged elements or inappropriate setup during preliminary installment.
One more regular concern is irregular product packaging speeds, commonly created by mechanical wear or insufficient maintenance. Irregularity in rate can cause traffic jams, creating hold-ups and minimizing overall efficiency. In addition, poor training of personnel can aggravate these issues, as operators may not totally comprehend machine performances or troubleshooting techniques.
Furthermore, material jams are a common occurrence, often because of inaccurate product requirements or international objects blocking the maker's path. Such jams can stop production, necessitating immediate intervention to clear the obstruction and resume procedures.
Last but not least, digital faults, consisting of software program glitches or sensing unit failings, can hamper device performance - packaging machine repair service. These problems require timely focus, as they can result in extensive downtime otherwise attended to promptly. Understanding these typical issues is vital for keeping optimum efficiency and lessening disruptions in product packaging operations
Analysis Methods for Fixings
Applying efficient diagnostic strategies is critical for recognizing and solving issues in packaging machines. A methodical approach to diagnostics permits professionals to identify the source of malfunctions effectively, consequently minimizing downtime and enhancing functional performance.
One of the key methods involves aesthetic evaluations, where specialists examine the maker for any type of apparent indications of wear, imbalance, or damage. These tools assess maker efficiency data, supplying insights into abnormalities that may not be promptly visible.
One more crucial method is performing functional examinations. By methodically operating different components of the device, service technicians can observe efficiency disparities, helping to isolate damaged parts. Additionally, carrying out resonance analysis and thermal imaging can uncover surprise problems, such as misaligned belts or overheating bearings, which are often precursors to more substantial failings.
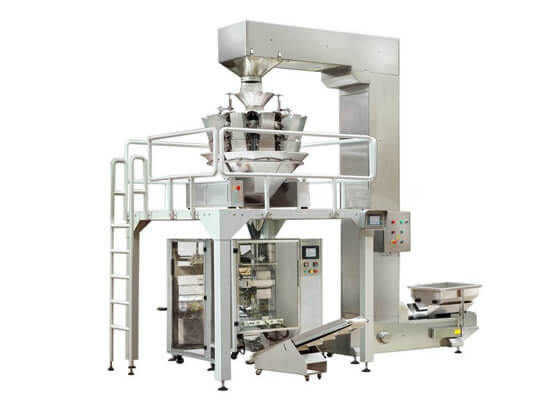
Step-by-Step Repair Work Procedures
A comprehensive repair work treatment is crucial for recovering capability to malfunctioning packaging makers. The process begins with a detailed evaluation of the problem, utilizing diagnostic strategies to determine the source of the breakdown. Once recognized, collect the required devices and replacement components to assist in the repair.
Following, ensure that the equipment is powered off and disconnected from its power resource to assure security throughout the repair service. Recording the equipment's configuration before disassembly can aid in reassembly - packaging machine repair service. Meticulously eliminate any kind of panels or covers to access the malfunctioning elements, noting any certain screws or fasteners that call for attention
Replace or fix the malfunctioning parts according to the producer's requirements, guaranteeing that all links are safe and secure. After reassembly, conduct an aesthetic evaluation to verify that all parts are properly installed which there are no loosened connections.
Once the equipment is reconstructed, reconnect the power and conduct examinations to ensure correct functionality. Screen the maker throughout procedure to recognize any recurring concerns. Record the repair service process, including parts changed and observations, to inform future maintenance initiatives. This careful approach advertises optimum equipment efficiency and long life.
Preventive Maintenance Practices
Maintaining the functionality of packaging machines is not solely dependent on responsive fixing procedures; proactive preventive upkeep methods play a substantial duty in guaranteeing their longevity and efficiency (packaging machine repair service). By implementing an organized precautionary maintenance program, operators can identify prospective problems prior to they escalate right into costly breakdowns
Service technicians need to regularly check components such as belts, gears, and sensing units for wear and tear. Additionally, cleaning up equipments to eliminate dust and particles is necessary for optimal performance and to stop contamination of items.
Educating staff on correct usage and handling of packaging machines can likewise lessen the threat of operational mistakes that might cause devices failure. Establishing an upkeep routine that includes regular checks and replacements of vital components can dramatically expand the article lifespan of the equipment.
Documenting all maintenance activities not just help in tracking the health and wellness of the equipment but likewise adheres to regulatory requirements. By prioritizing precautionary maintenance, companies can guarantee their product packaging equipments operate at peak efficiency, eventually boosting efficiency and lowering downtime.
Devices and Resources for Technicians
Outfitting technicians with the right tools and resources is essential for effective product packaging equipment repair service and maintenance. A well-stocked toolkit should include accuracy instruments such as wrenches, calipers, and screwdrivers customized for details equipment use this link components. Furthermore, analysis devices like multimeters and oscilloscopes make it possible for service technicians to determine electric issues swiftly and accurately.

Additionally, buying software services for devices monitoring can improve anticipating maintenance methods. These applications evaluate device performance information, signaling technicians to potential concerns before they intensify.
Connecting with peers and signing up with industry forums can facilitate understanding sharing and best methods amongst technicians, fostering a joint setting for continual knowing. Lastly, maintaining connections with vendors guarantees fast access to spare components and specialized tools, decreasing downtime throughout repair services. By leveraging these sources and devices, technicians can boost their efficiency and performance in preserving ideal performance of packaging devices.
Conclusion

Reliable packaging machine repair is see it here vital for keeping functional continuity and product quality in today's fast-paced production setting.Product packaging devices, important for reliable manufacturing lines, commonly encounter a number of typical problems that can interrupt operations.An extensive repair service treatment is necessary for bring back capability to malfunctioning product packaging makers.Equipping specialists with the right devices and resources is important for effective packaging maker fixing and maintenance.In final thought, effective product packaging machine repair service strategies are important for keeping optimal performance and reducing operational downtime.
Comments on “Packaging Machine Repair Service: Avoid Expensive Break Downs with Expert Help”